Die Operatoren im Steel Service Center (SSC) arbeiten nach Total Productive Maintenance (TPM), als Teil der Lean Six Sigma-Arbeitsmethode. Dieser Ansatz hilft ihnen dabei, deren Arbeit engagierter und effizienter auszuführen. Im Rahmen von TPM wurde ein Testprojekt mit Decoiler 3 gestartet. Produktionsleiter Riny van de Donk und Teamleiter Johan Groenen machen eine zwischenzeitliche Bestandsaufnahme. Bei der neuen Arbeitsweise mit Decoiler 3 wird die SMED-Methode eine wichtige Rolle spielen. SMED ist die englische Abkürzung für Single-Minute Exchange of Die. Frei übersetzt: Sachen innerhalb weniger Minuten austauschen.
„SMED ist eine Methode, mit der Umstellungszeiten von Maschinen - in unserem Fall Decoiler 3 - verkürzt werden. Das System stammt aus Japan, wo es erfolgreich bei Toyota eingesetzt wurde. Indem wir das Umstellungsverfahren mit „SMED“ gründlich analysieren und die dadurch gewonnene Zeit in ein häufigeres Umstellen investieren, können kleine Serien flexibler hergestellt werden. Hierdurch werden die Durchlaufzeiten verkürzt und unsere Lieferzuverlässigkeit drastisch erhöht“, erläutern Riny und Johan.
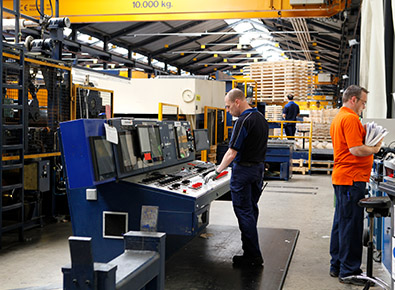
Umlaufgeschwindigkeit erhöhon
„Wir erhöhen die Umlaufgeschwindigkeit, um die Produktion der Maschine zu verbessern. Es ist also keinesfalls eine Kontrolle der Arbeitsweise und des Einsatzes der Operatoren. Es geht darum, dass sie ihren eigenen Mehrwert verstehen und ihre eigene Arbeit inhaltlich interessanter wird. Wir möchten Sachen gemeinsam einfacher und verständlicher gestalten. Wir arbeiten nun daran, die Probleme aus dem Verfahren zu filtern.“
Boxenstopp
Johan und Kollegin Marika van der Molen machen regelmäßig Filmaufnahmen bei Decoiler 3. „So registrieren wir, was genau passiert, bevor der Decoiler mit der tatsächlichen Produktion beginnt. Das Austauschen am Decoiler kostet Zeit, aber auf diesem Gebiet können wir Fortschritte machen. Das Anbringen von Folie auf den Blechen erweist sich ebenfalls als schwierige Aufgabe und auch hier möchten wir die Dinge möglichst effizient angehen.
Ferner messen wir die Zeit vom ersten guten Produkt bis zum letzten guten Produkt. Man kann es mit einem Boxenstopp in der Formel 1 vergleichen. Hier wurde eine essenzielle Handlung - der Reifenwechsel - bis auf ein paar Sekunden reduziert“, so Johan. „Die Operatoren freuen sich über diese Arbeitsweise. Es verleiht deren Arbeit mehr Inhalt und sie sehen Ergebnisse. Wir haben in der vormaligen TD-Werkstatt in Kürze einen Raum, in dem wir Dinge besprechen und die Videos anschauen. Wenn Menschen sehen, was sie eigentlich machen, sehen sie die Dinge oft ganz anders. Wenn man bestimmte Angelegenheiten visuell registriert, lernt man mehr!“
Komplett digital
Ziel ist es, das Produktionsverfahren bei den Decoilern komplett digital zu gestalten. „Die Steuerung wurde bereits modernisiert und das TPM-Gebäude nimmt immer mehr Form an. Man hört auch Bemerkungen, dass es bei Decoiler 3 für die Bedienung mehr Bildschirme als Knöpfe gibt.
Alles nimmt konkrete Formen an“, stellt Riny zufrieden fest. „Man merkt schon, dass sich manche Leute an die englischen Begriffe gewöhnen müssen, die sich auch ins SSC schleichen, aber das ist nur eine Frage der Zeit!“